Abstract
In order to reduce the uncertainty in the selection of geometric tolerance items, a qualitative method for top-down transfer of geometric tolerance items is proposed. The assembly joint which is composed of two mating surfaces with functional requirements or structural constraints is acted as the basis of geometric tolerance items transmission. According to the structural characteristics, the assembly joints are divided into meta-assembly joints and composite assembly joints, and the priority rules for assembly joints are proposed. The transfer path of part-level geometric tolerance items is established according to the functional requirements and structural constraints among parts. On this basis, by adding information about the composition and constraint types of assembly joints between parts and the position constraint relationship of the general structure surface in the part, the transfer path of part-level geometric tolerance items is extended to the transfer path of geometric feature surface-level. With the development of product design, the initial functional requirements will be transformed into structural constraints between parts and geometric feature surfaces, and the structural transformation model of functional requirements is constructed. The generation specifications of geometric tolerance items based on structural constraints and the transfer specifications of datums are established. And based on the above specifications, the mapping relationship between functional requirements, structural constraints, and geometric tolerance items is defined. The synchronous transmission of geometric tolerance items along with the product design process are realized which provides an effective analysis tool for the top-down design of geometric tolerance items. Finally, the effectiveness of the method is verified by taking the transmission parts and connection parts in the crankshaft-piston mechanism as an example.












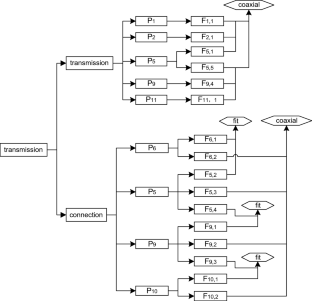



Similar content being viewed by others
Availability of data and materials
All data generated or analyzed during this study are included in this published article.
References
Maroua G, Mehdi T, Nizar A, Eric P (2017) A CAD method for tolerance allocation considering manufacturing difficulty based on FMECA tool. Int J Adv Manuf Technol 91:2435–2446
Mehdi T, Maroua G, Nizar A (2019) Integrated CAD tolerancing model based on difficulty coefficient evaluation and Lagrange multiplier. Int J Adv Manuf Technol 101:2519–2532
Hallmann M, SchleichB WS (2020) Form tolerance allocation to tolerance-cost optimisation: a comprehensive literature review. Int J Adv Manuf Technol 107:4859–4912
Anselmetti B (2006) Generation of functional tolerancing based on positioning features. Comput Aided Des 38(8):902–919
Cao Y, Zhang H, Li B, Wu Z, Yang J (2013) Study on functional specification scheme on interface based on positioning features. Proc IMechE Part B J Eng Manuf 227(5):745–753
Mao J, Zong Y (2015) Assembly tolerance modeling based on generalized directed graph. Procedia Cirp 27:318–323
Yang JX, Xu XS, Cao YL, Liu YC (2010) Functional tolerance specification design based on assembly positioning. Chin J Mech Eng En 46(02):1–8
Anselmetti B, Chavanne R, Yang JX, Anwer N (2010) Quick GPS: a new CAT system for single-part tolerancing. Comput Aided Design 42(9):768–780
Gong JF, Ding LP, Chen BF, Chen WL, Bai XY (2016) Tolerance specification design for parts based on positioning features. Automat Constr 5:16–21
Zhang Y, Li ZB, Gao JM, Hong J (2011) New reasoning algorithm for assembly tolerance specifications and corresponding tolerance zone types. Comput Aided Des 43(12):1606–1628
Armillotta A (2013) A method for computer-aided specification of geometric tolerances. Comput Aided Des 45(12):1604–1616
Jiang K, Liu JH, Ning RX, Guo CY (2015) Geometric tolerances reasoning and its specification verification based on polychromatic sets theory. Comput Integr Manuf 21(03):593–605
Cao Y, Zhao Q, Liu T, Ren L, Yang J (2018) The strategy of datum reference frame selection based on statistical learning. ASME Trans J Comput Inf Sci Eng 18(2):021002
Jaballi K, Bellacicco A, Louati J, Riviere A, Haddar M (2011) Rational method for 3D manufacturing tolerancing synthesis based on the TTRS approach “R3DMTSyn”. Comput Ind 62(5):541–554
Zhang KF, Li Y, Tang SL (2010) An integrated modeling method of unified tolerance representation for mechanical product. Int J Adv Manuf Technol 46:217–226
Zhang KF, Li Y, Shao Y, Yang HC (2005) A unified tolerance model for part based on key features and graph. J Northwestern Polytech Univ 05:106–110
Patalano S, Vitolo F, Gerbino S, Lanzotti A (2018) A graph-based method and a software tool for interactive tolerance specification. Procedia CIRP 75:173–178
Qin YC, Zhong YR, Chang L, Huang MF (2013) Automatic generation of tolerance types based on geometric tolerance description logic. Comput Integr Manuf 19(07):1490–1499
Qin YC, Lu WL, Liu XJ, Huang MF, Zhou LP, Jiang XQ (2015) Description logic-based automatic generation of geometric tolerance zones. Int J Adv Manuf Technol 79(5-8):1221–1237
Qin YC, Lu WL, Qi QF, Liu XJ, Huang MF, Scott PJ, Jiang XQ (2018) Towards a tolerance representation model for generating tolerance specification schemes and corresponding tolerance zones. Int J Adv Manuf Technol 97:1801–1821
Zhong YR, Qin YC, Huang MF, Lu WL, Gao WX, Du YL (2013) Automatically generating assembly tolerance types with an ontology-based approach. Comput Aided Des 45(11):1253–1275
Zhong YR, Qin YC, Huang MF, Lu WL, Chang L (2014) Constructing a meta-model for assembly tolerance types with a description logic based approach. Comput Aided Des 48:1–16
Zhao Q, Cao Y, Liu T, Ren L, Yang J (2018) Tolerance specification of the plane feature based on the axiomatic design. Proc Inst Mech Eng C J Mech Eng Sci 233:1481–1492
Zhao QJ, Li TK, Cao YL, Yang JX, Jiang XQ (2020) A computer-aided tolerance specification method based on multiple attributes decision-making. Int J Adv Manuf Technol 111:1735–1750
Goetz S, Schleich B, Wartzack S (2018) A new approach to first tolerance evaluations in the conceptual design stage based on tolerance graphs. Procedia CIRP 75:167–172
Sarigecili MI, Roy U, Rachuri S (2014) Interpreting the semantics of GD&T specifications of a product for tolerance analysis. Comput Aided Des 47:72–84
Shi X, Tian X, Wang G, Zhang M, Zhao D (2018) A simplified model for assembly precision information of complex products based on tolerance semantic relations. Sustainability 10(12):1–19
Goetza S, Schleicha B (2020) Ontology-based representation of tolerancing and design knowledge for an automated tolerance specification of product concepts. Procedia CIRP 92:194–199
Wang HQ, Lv ZY, Zhang X, Tang CT (2018) GD & T semantic information interpretation for tolerance analysis. Comput Integr Manuf 24(04):994–1006
Qin Y, Lu W, Qi Q, Liu X, Huang M, Scott PJ, Jiang X (2018) Towards an ontology-supported case-based reasoning approach for computer-aided tolerance specification. Knowl-Based Syst 141:129–147
Funding
The authors would like to acknowledge the financial support from the National Natural Science Foundation of China (No. 51775239) and Natural Science Foundation Project of Shandong Province (ZR2020ME137).
Author information
Authors and Affiliations
Contributions
MA performed the design of method and wrote the manuscript; YANG and MA conceived and designed the study; LI, LIU, WANG, and GAO helped perform the analysis with constructive discussions. All authors read and approved the manuscript.
Corresponding author
Ethics declarations
Ethical approval
Not applicable.
Consent to participate
Not applicable.
Consent to publish
Not applicable.
Competing interests
The authors declare no competing interest.
Additional information
Publisher’s note
Springer Nature remains neutral with regard to jurisdictional claims in published maps and institutional affiliations.
Rights and permissions
About this article
Cite this article
Ma, N., Yang, B., Li, J. et al. Transfer method of geometric tolerance items based on assembly joints. Int J Adv Manuf Technol 117, 1689–1708 (2021). https://doi.org/10.1007/s00170-021-07598-y
Received:
Accepted:
Published:
Issue Date:
DOI: https://doi.org/10.1007/s00170-021-07598-y