Roman concrete
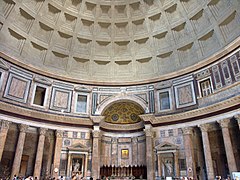

Roman concrete, also called opus caementicium, was used in construction in ancient Rome. Like its modern equivalent, Roman concrete was based on a hydraulic-setting cement added to an aggregate.
Many buildings and structures still standing today, such as bridges, reservoirs and aqueducts, were built with this material, which attests to both its versatility and its durability. Its strength was sometimes enhanced by the incorporation of pozzolanic ash where available (particularly in the Bay of Naples). The addition of ash prevented cracks from spreading. Recent research has shown that the incorporation of mixtures of different types of lime, forming conglomerate "clasts" allowed the concrete to self-repair cracks.[1]
Roman concrete was in widespread use from about 150 BC;[2] some scholars believe it was developed a century before that.[3]
It was often used in combination with facings and other supports,[4] and interiors were further decorated by stucco, fresco paintings, or coloured marble. Further innovative developments in the material, part of the so-called concrete revolution, contributed to structurally complicated forms. The most prominent example of these is the Pantheon dome, the world's largest and oldest unreinforced concrete dome.[5]
Roman concrete differs from modern concrete in that the aggregates often included larger components; hence, it was laid rather than poured.[6] Roman concretes, like any hydraulic concrete, were usually able to set underwater, which was useful for bridges and other waterside construction.
Historic references
[edit]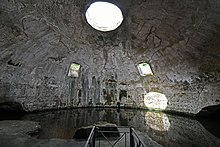
Vitruvius, writing around 25 BC in his Ten Books on Architecture, distinguished types of materials appropriate for the preparation of lime mortars. For structural mortars, he recommended pozzolana (pulvis puteolanus in Latin), the volcanic sand from the beds of Pozzuoli, which are brownish-yellow-gray in colour in that area around Naples, and reddish-brown near Rome. Vitruvius specifies a ratio of 1 part lime to 3 parts pozzolana for mortar used in buildings and a 1:2 ratio for underwater work.[10][11]
The Romans first used hydraulic concrete in coastal underwater structures, probably in the harbours around Baiae before the end of the 2nd century BC.[12] The harbour of Caesarea is an example (22-15 BC) of the use of underwater Roman concrete technology on a large scale,[10] for which enormous quantities of pozzolana were imported from Puteoli.[13]
For rebuilding Rome after the fire in 64 AD which destroyed large portions of the city, Nero's new building code largely called for brick-faced concrete.[citation needed] This appears to have encouraged the development of the brick and concrete industries.[10]

Material properties
[edit]Roman concrete, like any concrete, consists of an aggregate and hydraulic mortar, a binder mixed with water that hardens over time. The composition of the aggregate varied, and included pieces of rock, ceramic tile, lime clasts, and brick rubble from the remains of previously demolished buildings. In Rome, readily available tuff was often used as an aggregate.[14]
Gypsum and quicklime were used as binders.[2] Volcanic dusts, called pozzolana or "pit sand", were favoured where they could be obtained. Pozzolana makes the concrete more resistant to salt water than modern-day concrete.[15] Pozzolanic mortar had a high content of alumina and silica.
Research in 2023 found that lime clasts, previously considered a sign of poor aggregation technique, react with water seeping into any cracks. This produces reactive calcium, which allows new calcium carbonate crystals to form and reseal the cracks.[16] These lime clasts have a brittle structure that was most likely created in a "hot-mixing" technique with quicklime rather than traditional slaked lime, causing cracks to preferentially move through the lime clasts, thus potentially playing a critical role in the self-healing mechanism.[1]
Concrete and, in particular, the hydraulic mortar responsible for its cohesion, was a type of structural ceramic whose utility derived largely from its rheological plasticity in the paste state. The setting and hardening of hydraulic cements derived from hydration of materials and the subsequent chemical and physical interaction of these hydration products. This differed from the setting of slaked lime mortars, the most common cements of the pre-Roman world. Once set, Roman concrete exhibited little plasticity, although it retained some resistance to tensile stresses.

The setting of pozzolanic cements has much in common with setting of their modern counterpart, Portland cement. The high silica composition of Roman pozzolana cements is very close to that of modern cement to which blast furnace slag, fly ash, or silica fume have been added.
The strength and longevity of Roman 'marine' concrete is understood to benefit from a reaction of seawater with a mixture of volcanic ash and quicklime to create a rare crystal called tobermorite, which may resist fracturing. As seawater percolated within the tiny cracks in the Roman concrete, it reacted with phillipsite naturally found in the volcanic rock and created aluminous tobermorite crystals. The result is a candidate for "the most durable building material in human history". In contrast, modern concrete exposed to saltwater deteriorates within decades.[17][18][19]
The Roman concrete at the Tomb of Caecilia Metella is another variation higher in potassium that triggered changes that "reinforce interfacial zones and potentially contribute to improved mechanical performance".[20]
Seismic technology
[edit]
For an environment as prone to earthquakes as the Italian peninsula, interruptions and internal constructions within walls and domes created discontinuities in the concrete mass. Portions of the building could then shift slightly when there was movement of the earth to accommodate such stresses, enhancing the overall strength of the structure. It was in this sense that bricks and concrete were flexible. It may have been precisely for this reason that, although many buildings sustained serious cracking from a variety of causes, they continue to stand to this day.[21][10]
Another technology used to improve the strength and stability of concrete was its gradation in domes. One example is the Pantheon, where the aggregate of the upper dome region consists of alternating layers of light tuff and pumice, giving the concrete a density of 1,350 kilograms per cubic metre (84 lb/cu ft). The foundation of the structure used travertine as an aggregate, having a much higher density of 2,200 kilograms per cubic metre (140 lb/cu ft).[22][10]
Modern use
[edit]Scientific studies of Roman concrete since 2010 have attracted both media and industry attention.[23] Because of its unusual durability, longevity, and lessened environmental footprint, corporations and municipalities are starting to explore the use of Roman-style concrete in North America. This involves replacing the volcanic ash with coal fly ash that has similar properties. Proponents say that concrete made with fly ash can cost up to 60% less, because it requires less cement. It also has a reduced environmental footprint, due to its lower cooking temperature and much longer lifespan.[24] Usable examples of Roman concrete exposed to harsh marine environments have been found to be 2000 years old with little or no wear.[25] In 2013, the University of California Berkeley published an article that described for the first time the mechanism by which the suprastable calcium-aluminium-silicate-hydrate compound binds the material together.[26] During its production, less carbon dioxide is released into the atmosphere than any modern concrete production process.[27] It is no coincidence that the walls of Roman buildings are thicker than those of modern buildings. However, Roman concrete was still gaining its strength for several decades after construction had been completed.[17]
See also
[edit]- Energetically modified cement (EMC) – Class of cements, mechanically processed to transform reactivity
- Geopolymer – Polymeric Si–O–Al framework similar to zeolites but amorphous
- Roman brick – Style of brick used in Ancient Roman architecture
- Roman cement – Cement made by burning septaria, unrelated to ancient Rome
- Pozzolanic activity – Capacity of silica-rich materials to react with calcium hydroxyde to form calcium silicate hydrates
- Tobermorite – Inosilicate alteration mineral in metamorphosed limestone and in skarn
Literature
[edit]- Adam, Jean-Pierre; Mathews, Anthony (2014). Roman Building. Florence: Taylor & Francis. ISBN 9780203984369.
- Lancaster, Lynne C. (2009). Concrete Vaulted Construction in Imperial Rome: innovations in context. Cambridge University Press. ISBN 9780521842020.
- Lechtman, Heather; Hobbs, Linn (1986). "Roman Concrete and the Roman Architectural Revolution". In W.D. Kingery (ed.). Ceramics and Civilization. Vol. 3: High Technology Ceramics: Past, Present, Future. American Ceramics Society. ISBN 091609488X.
- MacDonald, William Lloyd (1982). The Architecture of the Roman Empire, v.2, an Urban Appraisal. New Haven: Yale University Press. ISBN 9780300034561.
References
[edit]- ^ a b Chandler, David L. (6 January 2023). "Riddle solved: Why was Roman concrete so durable?". MIT News. Archived from the original on 21 January 2023.
- ^ a b "National Pozzolan Association: The History of Natural Pozzolans". pozzolan.org. Retrieved 2021-02-21.
- ^ Boëthius, Axel; Ling, Roger; Rasmussen, Tom (1978). "Etruscan and Early Roman Architecture". Yale/Pelican history of art. Yale University Press. pp. 128–129. ISBN 978-0300052909.
- ^ "Aqua Clopedia, a picture dictionary on Roman aqueducts: Roman concrete / opus caementicium". romanaqueducts.info. Retrieved 2023-01-24.
- ^ Moore, David (February 1993). "The Riddle of Ancient Roman Concrete". S Dept. of the Interior, Bureau of Reclamation, Upper Colorado Region. Retrieved 20 May 2013.
- ^ Henig, Martin, ed. (1983). A Handbook of Roman Art. Phaidon. p. 30. ISBN 0714822140.
- ^ "Baiae, historic site, Italy". Encyclopedia Britannica.
- ^ Lancaster 2009, p. 40.
- ^ Mark, Robert; Hutchinson, Paul (March 1986). "On the Structure of the Roman Pantheon". The Art Bulletin. 68 (1). New York, NY: College Art Association: 24. doi:10.2307/3050861. JSTOR 3050861.
- ^ a b c d e Lechtman & Hobbs 1986.
- ^ Vitruvius. De Architectura, Book II:v,1; Book V:xii2.
- ^ Oleson et al., 2004, The ROMACONS Project: A Contribution to the Historican and Engineering Analysis of the Hydrauilc Concrete in Roman Maritime Structures, International Journal of Nautical Archaeology 33.2: 199-229
- ^ Hohlfelder, R. 2007. "Constructing the Harbour of Caesarea Palaestina, Israel: New Evidence from ROMACONS Field Campaign of October 2005". International Journal of Nautical Archaeology 36:409-415.
- ^ "Rome's Invisible City". BBC One. Retrieved 6 July 2017.
- ^ Wayman, Erin (16 November 2011). "The Secrets of Ancient Rome's Buildings". Smithsonian.com. Retrieved 24 April 2012.
- ^ Seymour, Linda; et al. (2023). "Hot mixing: Mechanistic insights into the durability of ancient Roman concrete". Science Advances. 9 (1): eadd1602. Bibcode:2023SciA....9D1602S. doi:10.1126/sciadv.add1602. hdl:1721.1/147056. PMC 9821858. PMID 36608117. S2CID 255501528.
- ^ a b Guarino, Ben (4 July 2017). "Ancient Romans made world's 'most durable' concrete. We might use it to stop rising seas". The Washington Post.
- ^ Jackson, Marie D.; Mulcahy, Sean R.; Chen, Heng; Li, Yao; Li, Qinfei; Cappelletti, Piergiulio; Wenk, Hans-Rudolf (2017). "Phillipsite and Al-tobermorite mineral cements produced through low-temperature water-rock reactions in Roman marine concrete". American Mineralogist. 102 (7): 1435–1450. Bibcode:2017AmMin.102.1435J. doi:10.2138/am-2017-5993CCBY. ISSN 0003-004X.
- ^ McGrath, Matt (4 July 2017). "Scientists explain ancient Rome's long-lasting concrete". BBC News. Retrieved 6 July 2017.
- ^ Ouellette, Jennifer (1 January 2022). "Noblewoman's tomb reveals new secrets of ancient Rome's highly durable concrete". Ars Technica. Retrieved 5 January 2022.
- ^ MacDonald 1982, fig. 131B.
- ^ K. de Fine Licht, The Rotunda in Rome: A Study of Hadrian's Pantheon. Jutland Archaeological Society, Copenhagen, 1968, pp. 89–94, 134–35
- ^ "Fixing Canada's Infrastructure with Volcanoes". Trebuchet Capital Partners Research. 15 October 2015. Retrieved 19 August 2016.
- ^ Patrick, Neil (6 September 2016). "By 25 BC, ancient Romans developed a recipe for concrete specifically used for underwater work which is essentially the same formula used today". The Vintage News.
- ^ M. D. Jackson, S. R. Chae, R. Taylor, C. Meral, J. Moon, S. Yoon, P. Li, A. M. Emwas, G. Vola, H.-R. Wenk, and P. J. M. Monteiro, "Unlocking the secrets of Al-tobermorite in Roman seawater concrete", American Mineralogist, Volume 98, pp. 1669–1687, 2013.
- ^ Jackson, Marie D.; Moon, Juhyuk; Gotti, Emanuele; Taylor, Rae; Chae, Sejung R.; Kunz, Martin; Emwas, Abdul-Hamid; Meral, Cagla; Guttmann, Peter; Levitz, Pierre; Wenk, Hans-Rudolf; Monteiro, Paulo J. M. (28 May 2013). "Material and Elastic Properties of Al-Tobermorite in Ancient Roman Seawater Concrete". Journal of the American Ceramic Society. 96 (8): 2598–2606. doi:10.1111/jace.12407. Retrieved November 4, 2023.
- ^ "Renaissance of Roman Concrete: Cutting carbon emissions". constructionspecifier.com. 29 December 2016. Retrieved June 27, 2022.
External links
[edit]- Hunt, Katie (2023-01-06). "Why Roman concrete outlasts its modern counterpart". CNN. Retrieved 2023-01-07.
- Preuss, Paul (2013-06-04). "Roman Seawater Concrete Holds the Secret to Cutting Carbon Emissions". Berkeley Lab News Center. Retrieved 2023-01-07.
- Wayman, Erin (2011-11-16). "The Secrets of Ancient Rome's Buildings". Smithsonian Magazine. Retrieved 2023-01-07.