by Bill Perry
Bell engineers in Mirabel, Quebec, garnered lots of media coverage for the flight of a Bell 429 demonstrator helicopter fitted with the company’s recently-developed electrically distributed anti-torque (EDAT) system in February 2020.
The electrically distributed anti-torque (EDAT) system aims to reduce noise and operating costs while increasing safety. The system replaces a helicopter’s mechanical anti-torque system – gearboxes, driveshafts and the tail rotor hub and blades – with fans driven by electric motors.
Asked in January 2021 when Bell plans to commercialize the system, Eric Sinusas, the company’s director for commercial development programs said, “We don’t yet have a date for entry into service. We’re maturing the technology and continuing to optimize it.”
The electrically distributed anti-torque (EDAT) system uses four fans in a two-by-two pattern within an integral shroud. Turning each fan are Safran-made motors with built-in electronics. Two generators power the four motors, each generator powers two motors, respectively. From the cockpit, the pilot can monitor each fan’s rpm.
The pilot controls the EDAT system’s fans via pedals, similar to yaw control in a conventional helicopter design. But the pedals and Safran motors are linked via fly-by-wire.
Bell’s engineers have a pedigree with fly-by-wire, having successfully flew the 525 Relentless, the world’s first commercial helicopter equipped with fly-by-wire flight controls at the company’s Amarillo, Texas, facility in 2015. While the 525 is not yet fully certified, Bell is accumulating data and vetting assumptions about the capability of fly-by-wire for reducing failures and improving safety.
Industry observers believe Bell is likely being very conservative, even moving slowly at this point, and expanding its testing envelope incrementally to ensure the validity of EDAT. Meanwhile the potential benefits of the system are eagerly awaited by the aviation community. When asked about EDAT, one long-time helicopter pilot qualified to fly dozens of different aircraft said, “Helicopter controls are pretty damn complex. EDAT is ingenious, especially if it turns out to be safer, lighter and simpler.”
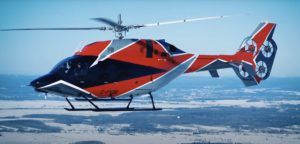
The media attention at the beginning of 2020 was a departure from Bell’s intended plans for demonstrating the technology. According to Bell representatives, a person captured footage of the EDAT-equipped 429 flying near its Mirabel facility and posted images on social media during January 2020. In response to the reveal, Bell made a formal announcement about EDAT several weeks later.
The official reveal was important for not only being a first-in-the-world demonstration of the technology, but also proof of passing a vital developmental milestone – that the EDAT system’s technology, including its handling qualities, worked.
According to Sinusas, further testing of EDAT is focusing on optimization of the system particularly at higher altitudes, in inclement weather and in assessing how it can help reduce pilot workload. The overall drivers that are guiding the development of the EDAT system are to reduce both noise and operating costs, while also improving safety, Sinusas emphasizes.
Prioritizing noise reduction
“Electrified systems are a running theme these days,” said Sinusas, “But what drove the step-change that led to EDAT was asking ourselves how to reduce noise.”
As the modified 429 moves aloft at increasingly faster airspeed, the EDAT fans reduce rpm and consequently the amount of noise. One of the main causes of noise in a helicopter is the tip speed of its tail rotor blades, which in some models can reach 650 feet per second. For instance, Airbus states its H145 helicopter, which also features a shrouded tail rotor, produces around 85.8dB of noise during level flight.
For any helicopter, the loudest noise emanates from the tail rotors in a sideways condition, for example when the aircraft is hovering in a 35-knot broadside wind. That condition, says Bell, uses maximum thrust and the EDAT tail fans create the maximum amount of noise and speed.
Bell declined to quantify by how many decibels the EDAT fans have lowered noise compared to a conventional tail rotor and assembly, but Sinusas noted that the EDAT system has “significantly reduced noise”.
According to John Cox, CEO of aviation safety consulting firm Safety Operating Systems, the EDAT system’s ability to potentially reduce tail rotor noise “could be a big benefit for air tours, law enforcement and flying over-populated areas.”
A quieter solution
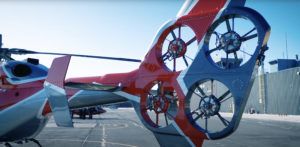
The engineers at Bell did consider designing different tip shapes to reduce the noise of its tail rotor blades but decided the biggest noise reduction would be achieved by reducing rotor tip speed.
The starting point was the fact that a helicopter does not use maximum thrust in all conditions. Meaning that effectively, tail rotors are over-designed to deal with worst-case scenarios. In response, Bell’s EDAT system offers a variable speed, fixed pitch solution.
While examining different approaches for tip speed and blade pitch, Bell’s engineers also looked at the EDAT system’s electrical make-up. The EDAT’s design meant having to change the speed of each fan quickly to control thrust – the bigger the fan, the more rotation and the more difficult it becomes to change speed quickly.
By designing smaller fans and more of them, it becomes easier to change speed and offer more reliability. In a conventional tail rotor system, each blade changes position dynamically, based on the pilot’s control and changes to the pitch of the blades or rotation of the rotor system in flight. In contrast, Bell’s EDAT system’s fans are rigidly mounted to the rotor output shaft.
Safran’s ENGINeUS motors, which output up to 500kW (670hp) are powering the EDAT’s fans. If a motor should fail, Thierry Sieg, Safran’s vice president of sales and marketing of electrical and power said, “there’s built-in redundancy with two other fans to mitigate failure.”
According to Sieg, Bell selected the ENGINeUS because its engineers were “interested in the maturity level and safety features”.
The ENGINEeUS motor is increasingly being used in aerospace applications. French aircraft developer Volt-Aero is using the motors in its hybrid-electric aircraft. In November 2020, Denver, Colorado-based aircraft developer Bye Aerospace announced it will be using the ENGINEeUS motors in the propulsion system of its forthcoming eFlyer all-electric training aircraft.
Bell has experimented with other electric fan-based anti-torque systems before, principally the FCX-001 concept, which engineers embedded in the helicopter’s tail boom and the company demonstrated in 2017. When asked why Bell was investing in the EDAT system when it had already demonstrated an electric fan-based anti-torque system with the FCX, Sinusas replied, “They are different concepts. FCX wasn’t maturing as a technology.”
Safety and operational costs
Alongside reducing noise, Sinusas claims the EDAT system enhances safety through adding redundancy. The aircraft can still produce anti-torque thrust if three of the four fans become inoperable. Also, says Bell, unlike traditional helicopters that continue to spin their tail rotors when the engine is running, the EDAT’s fans stop rotating as soon as there is friction on its skids. This adds safety for bystanders and ground crew.
A helicopter expert consulted for this article who has served as a test pilot noted the advantages of a shrouded fan – such as the Fenestron, or even a Kamov Ka-32, which has no tail rotor – include providing a safer working area for crews. But the pilot said the EDAT system’s capability to shut down the fans, while the engine runs, was taking safety to a higher level.
Cox from Safety Operations Systems said, “A significant hazard is loss of tail rotor effectiveness and anything that increases the capability of the tail rotor would certainly improve things. It’s the logical next step.”
In addition to lowering noise levels and boosting safety, Sinusas believes that once commercialized the EDAT concept should reduce helicopter operating costs. For example, the maintenance associated with fluid requirements for a conventional gearbox and bearings and the consequent wear on elastomeric bearings goes away. With an EDAT system, the only moving parts are in the motor and generator.
Industry insiders say certification could be challenging for the EDAT system. The FAA and Transport Canada will focus on failure modes. Helicopter certification standards are based on mechanically-driven tail rotors, so experts believe Bell will aim to convince Transport Canada and the FAA that the EDAT system is not just a safe concept, but safer than conventional systems.
Demonstrating those points, say experts, will include showing government regulators how pilots will interact with data such as the EDAT fans’ rpm and how the system architecture powers the fans.
However, Bell is the company that introduced the USA’s first civil certified helicopter in 1946, the Model 47. It does not lack experience with the certification process and is set on developing and refining its EDAT technology further.